Comprehending Exactly How a Chemical Defoamer Works to Improve Industrial Processes
Chemical defoamers play an essential duty in enhancing industrial processes by successfully minimizing foam-related challenges. Their ability to lower surface tension and disrupt bubble development equates right into smoother operations and improved performance. However, the systems behind their activity and the variety of readily available formulations require a closer assessment. Chemical Defoamer. Comprehending these aspects might disclose considerable understandings into not just boosting production however likewise achieving price financial savings across multiple sectors. What remains to be discovered is just how these defoamers can be customized to satisfy details functional demands.
What Is a Chemical Defoamer?
A chemical defoamer is a material especially developed to eliminate the development or minimize of foam in different commercial processes. Foaming can hinder manufacturing efficiency, influencing the top quality and performance of products in industries such as food and beverage, pharmaceuticals, and wastewater treatment. Defoamers are vital in these applications, as extreme foam can cause functional difficulties, such as overflow, lowered blending effectiveness, and prevented heat transfer.
The choice of a suitable defoamer is necessary, as different formulas may be tailored for particular processes or kinds of foam. Elements such as compatibility with various other ingredients, temperature level security, and the designated application play a substantial role in the efficiency of a defoamer.
Mechanisms of Defoaming Action
The systems of defoaming activity involve complex interactions in between the foam and the defoamer framework. When a defoamer is presented to a foaming system, it migrates swiftly to the surface of the foam bubbles, displacing the supporting agents that contribute to foam stability.
As smaller bubbles merge into larger ones, the overall stability of the foam diminishes. In addition, certain defoamers may contain hydrophobic components that enhance their capacity to undercut the foam by producing an obstacle that prevents bubble development. This double action-- surface tension decrease and destabilization-- permits an extra efficient failure of foam.
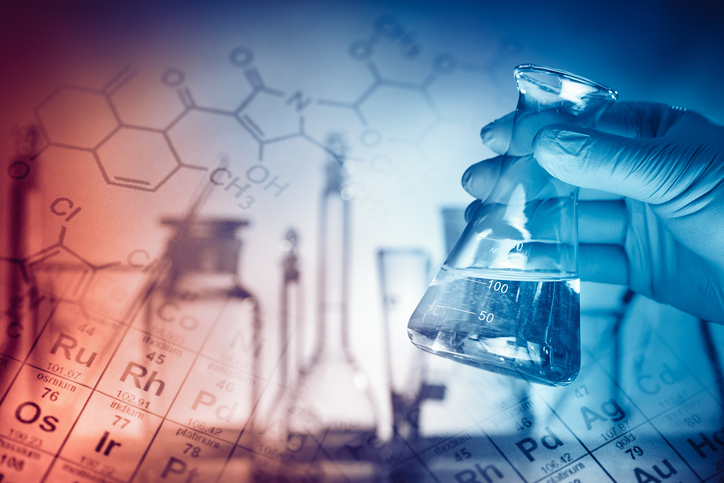
Furthermore, the thickness and spreading characteristics of the defoamer play crucial duties in its efficiency. A well-formulated defoamer will ensure quick migration and optimal performance, minimizing foam development throughout commercial procedures. By recognizing these mechanisms, markets can better pick and apply chemical defoamers to enhance operational performance and item high quality.
Types of Chemical Defoamers
Chemical defoamers can be classified into a number of types, each tailored to particular applications and foam difficulties. The main categories consist of silicone-based, non-silicone-based, and powder defoamers.
Silicone-based defoamers are highly efficient due to their capacity to spread rapidly across fluid surface areas. They supply superb foam suppression and stability, making them appropriate for different industrial applications, including adhesives and coatings. Non-silicone-based defoamers, on the other hand, typically rely on natural substances like fats or esters. These are specifically preferred in food and beverage industries due to their reduced toxicity and governing compliance.
Powder defoamers contain solid fragments that can be added to completely dry processes or solutions. They are typically utilized in processes where liquid defoamers might not be effective, giving a special remedy for specific applications, such as in the production of particular sorts of plastics or powders.
Additionally, each type click this of defoamer can be tailored with different ingredients to boost effectiveness, such as emulsifiers or surfactants, enabling versatility in resolving look at this site different lathering situations throughout multiple markets.
Applications in Industrial Processes
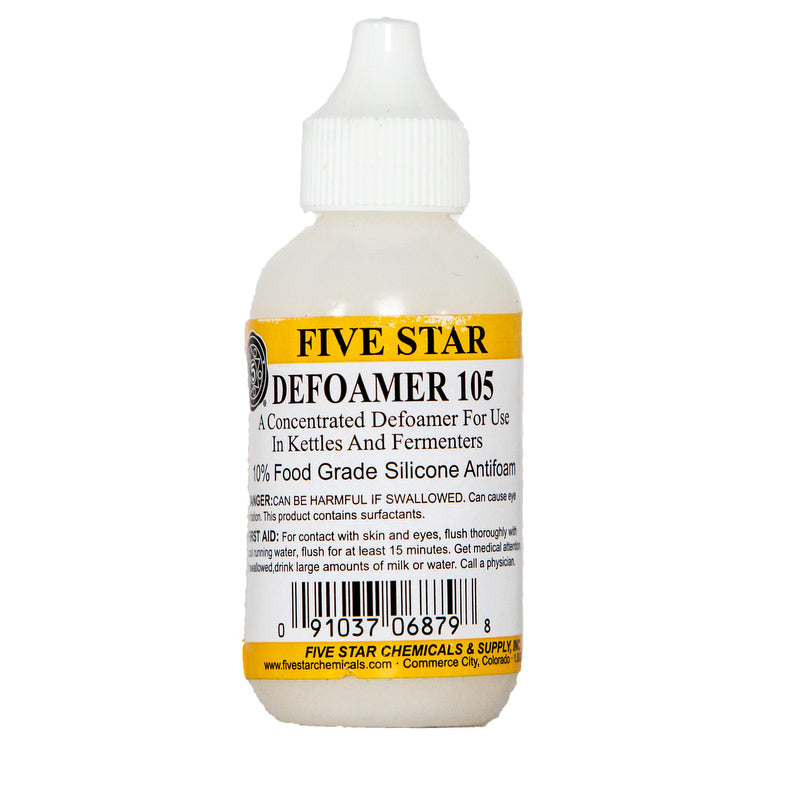
In the food and beverage industry, defoamers are crucial during the production of juices, beers, and dairy items, where extreme foam can impede mixing and filtering procedures. By reducing foam formation, defoamers aid keep constant item high quality and optimize handling times.
In pharmaceuticals, the presence of foam throughout the mixing and formula of medicines can impact dose precision and product stability. Defoamers make certain smooth procedures, therefore helping with the manufacturing of top quality drugs.
Wastewater therapy centers also depend on defoamers to manage frothing in oygenation tanks, which can or else lower treatment performance and make complex sludge handling. By effectively managing foam, these chemicals improve the total efficiency of therapy procedures and add to regulatory conformity.

Advantages of Utilizing Defoamers
While foam can present significant difficulties across various sectors, the use of defoamers see this here supplies various benefits that improve functional effectiveness and item integrity. Defoamers effectively lower or get rid of foam development, causing smoother manufacturing procedures and improved item top quality. This reduction in foam minimizes disturbances during manufacturing, permitting continual procedure and boosted throughput.
In addition, the application of defoamers can lead to set you back financial savings by decreasing the demand for excess resources and power consumption related to foam management. By enhancing the production procedure, producers can attain higher yields and lower waste, ultimately enhancing success.
Furthermore, defoamers add to much better devices efficiency. Foam buildup can result in obstructing, overflow, and devices wear, causing pricey downtime and maintenance. By protecting against these problems, defoamers extend the lifespan of equipment and decrease operational prices.
Verdict

A chemical defoamer is a material especially formulated to reduce or eliminate the development of foam in numerous commercial procedures. When a defoamer is introduced to a lathering system, it migrates quickly to the surface area of the foam bubbles, displacing the stabilizing representatives that add to foam security. A well-formulated defoamer will ensure fast movement and ideal performance, minimizing foam formation throughout commercial processes. Defoamers properly reduce or eliminate foam formation, leading to smoother production procedures and improved product high quality.In conclusion, chemical defoamers play an important role in improving commercial processes by efficiently reducing foam development.